The Ultimate Guide to Aluminum Casting: Professional Insights and Finest Practices
The Ultimate Guide to Aluminum Casting: Professional Insights and Finest Practices
Blog Article
The Top Methods for Aluminum Spreading That You Required to Know
From the conventional sand casting technique to the complex financial investment casting procedure, each strategy offers special benefits that provide to various task demands. As we browse through the leading techniques for light weight aluminum spreading, it comes to be noticeable that grasping these techniques is crucial for achieving ideal outcomes.
Sand Casting Technique
The Sand Spreading Strategy is a fundamental method in light weight aluminum spreading, commonly utilized for its cost-effectiveness and adaptability in creating elaborate steel forms. This method involves developing a mold constructed from compacted sand right into which liquified light weight aluminum is put, enabling it to take the shape and solidify of the mold and mildew. Among the key benefits of sand casting is its capacity to create complex geometries with fairly reduced tooling costs, making it an appealing choice for manufacturers wanting to create special elements.
In the sand casting process, a pattern of the last part is pressed into a great sand blend had within a flask. As soon as the pattern is eliminated, a cavity representing the final part's shape is left in the sand. Molten aluminum is then poured into the cavity, filling the room and taking on the accurate information of the pattern. After the aluminum cools down and strengthens, the sand mold is escaped, exposing the freshly cast light weight aluminum part. Sand casting is commonly utilized in different sectors, including automobile, aerospace, and art factories, because of its capacity to generate both large and small metal elements with complex layouts.

Investment Casting Process
An elaborate approach utilized in aluminum casting is the Financial investment Casting Refine, recognized for its capability to produce extremely outlined and detailed metal parts. Referred to as the lost-wax casting process, this technique dates back thousands of years and stays a prominent choice in numerous sectors due to its versatility and precision.
The financial investment casting procedure begins with the development of a wax pattern, which is coated with a ceramic covering to create a mold. The wax is after that melted out, leaving a cavity in the form of the preferred part. Molten aluminum is put right into the ceramic mold and mildew, loading the dental caries and taking on the intricate details of the original wax pattern.
This approach is favored for its capability to create complicated shapes with excellent surface area finish and dimensional accuracy. It is generally utilized in the production of aerospace components, jewelry, and commercial equipment where complex styles are required. The financial investment casting process uses high repeatability and can produce components with very little machining required, making it an affordable choice for several applications.
Long-term Mold Technique
Using a various technique from the Financial investment Casting Refine, the Permanent Mold Technique in aluminum casting offers a distinct technique for developing steel elements. In this technique, a reusable mold, typically made of steel or actors iron, is utilized to shape the molten light weight aluminum. The mold and mildew is preheated to a certain temperature before the light weight aluminum is put into it. The heat transfer from the liquified metal to the mold aids in strengthening the aluminum quickly, lowering the cooling time contrasted to sand casting.
Among the essential benefits of the Long-term Mold And Mildew Technique is the improved surface area finish and dimensional precision of the spreadings produced. This approach is also understood for its ability to generate high-strength light weight aluminum parts with regular quality. In addition, the reusable nature of the mold and mildew makes it an economical choice for medium to high volume production runs.
Die Casting Modern Technology
Utilizing advanced manufacturing processes, die casting technology offers an extremely reliable approach for producing intricate light weight aluminum parts. This strategy entails injecting molten aluminum into a steel mold and mildew, called a die, at high stress. The die is particularly developed to shape the aluminum right into the preferred kind, causing high accuracy and excellent surface finish.
Die casting offers several advantages. It enables the production of complex shapes with thin wall surfaces, limited resistances, and smooth surface areas, making it ideal for applications where visual appeals and precision are important. Furthermore, die casting enables rapid production prices, lowering total production time and expenses.
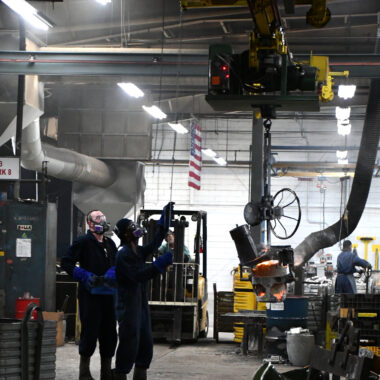
Lost Foam Spreading Approach
Die casting modern technology's performance and accuracy in generating light weight aluminum elements pave the way for exploring the Lost Foam Spreading Approach as a continue reading this corresponding manufacturing method. Lost Foam Casting, additionally recognized as evaporative pattern spreading, is a technique that uses foam patterns to create detailed light weight aluminum parts.
One of the key benefits of Lost Foam Spreading is its ability to produce intricate styles with elaborate details that might be challenging to achieve via typical casting methods. In addition, this method eliminates the demand for cores, minimizes machining operations, and permits tighter resistances. Lost Foam Casting is specifically appropriate for small to medium-sized light weight aluminum parts that call for high precision and intricate geometries. aluminum casting. As sectors remain to require lightweight yet durable elements, Lost Foam Casting verifies to be an important approach in the realm of light weight aluminum hop over to here casting.
Conclusion
To conclude, understanding the leading strategies for light weight aluminum casting is vital for achieving top notch results in the production procedure. Sand spreading, financial investment spreading, permanent mold, die casting, and shed foam casting are all efficient techniques for creating aluminum get rid of various degrees of intricacy. By grasping these strategies, producers can make sure that their items fulfill the desired specs and requirements for efficiency and durability.
From the conventional sand casting technique to the detailed financial investment spreading procedure, each technique offers distinct advantages that cater to different project demands.The Sand Casting Method is an essential technique in aluminum casting, widely utilized for its cost-effectiveness and flexibility in producing elaborate metal shapes. Lost Foam Casting, additionally recognized as evaporative pattern spreading, is an approach that makes use of foam patterns to produce complex aluminum parts. As industries proceed to require light-weight yet long lasting elements, Lost Foam Casting proves to be a valuable my explanation approach in the world of aluminum casting.
Sand spreading, financial investment casting, permanent mold, pass away spreading, and lost foam spreading are all reliable techniques for producing light weight aluminum components with different levels of intricacy.
Report this page